Modern Methods of Construction (MMC) are often perceived as a recent innovation, somewhat untested and experimental, yet the concept of offsite construction has been around for decades.
Saint-Gobain Off-Site Solutions
While significant strides are being made in the world of offsite, such as the use of advanced software tools and a greater focus on the use of low-embodied carbon materials, the fact remains that onsite, traditional thinking often prevails.
Will Jones, Marketing and Digital Director at Saint-Gobain Off-Site Solutions, argues that it is time for the social housing industry to overcome this misconception and embrace the numerous benefits of offsite construction now, to deliver real-time cost and efficiency savings.
Meeting an escalating housing crisis
According to a September 2024 survey conducted by national homelessness charity Crisis, Lloyds Banking Group and Simon Community Northern Ireland, the UK saw a net loss of over 12,000 social homes in England in 2023. It states that a quarter of renters will now spend between five and 10 years waiting for a social home. While the UK Government’s recent commitment to expand funding for affordable housing is certainly welcome, the UK is at a historically low base of housing delivery, and it will take time for the supply chain to recover. Offsite construction allows housing providers to shortcut a number of supply chain challenges, providing high-quality housing in a time and cost-effective way.
Homes England’s current Affordable Homes Programme sets a target for 25% of all homes to be built using MMC by 2026. However, a recent report from the National Housing Federation revealed that only 16% of all homes were constructed using these methods in 2023, indicating a significant gap between ambition and reality.
We can add to the mix the upcoming Future Homes Standard. Due to be rolled out next year, the standard, alongside other changes to regulations, should drive improvements in the long-term performance of homes across the UK. MMC and offsite construction have a role to play in delivering this lasting change that goes far beyond the usually cited benefit of speed on site.
MMC – proven and tested
So, what is holding the industry back from fully embracing the benefits of MMC when the benefits are both so numerous and generally well understood?
While offsite is certainly faster – in some cases, reducing build times by up to 40% compared to traditional methods – building components in a controlled factory environment also helps to minimise onsite defects, providing greater certainty in building performance and reducing the gap between as-designed and as-built performance. MMC also has the potential to provide more predictable costs through standardisation, bulk buying of materials, and fewer onsite delays – not to mention the array of options to improve a building’s energy performance through the application of advanced insulation techniques.
Rather than viewing MMC as an offsite variation of traditional construction techniques, the answer may lie in embracing MMC as an enabler to a more intelligent means of construction. MMC can be where the application of digital tools, fused with factory manufacture, helps housing providers realise improved accuracy, delivery efficiency and scalability of programmes.
AI-driven design and manufacturing
We see this in the growing traction of AI-optimised design. This can optimise building layouts and structural components for both cost efficiency and sustainability. By simulating multiple construction scenarios, AI algorithms help architects and engineers make data-driven decisions, reducing errors and material wastage. Small changes in building design can drive significant savings in the finished building and AI tools allow this to be checked and tested at pace long before manufacture starts.
Building Information Modelling (BIM)
Another key technology that has transformed the impact of MMC is Building Information Modelling (BIM). BIM allows for the creation of digital twins – highly-detailed 3D models of buildings that can be used to simulate the construction process before work even begins. These models allow teams to anticipate and resolve potential issues, such as structural conflicts or energy inefficiencies, in the virtual world before they become real-world problems.
While the use of BIM is not unique to MMC projects, by integrating BIM with the factory accuracy of offsite construction, developers can achieve greater certainty in project performance, reducing delays and unexpected costs.
Predictive maintenance and lifecycle management
Digital tools are not only valuable during construction but also throughout a building’s lifecycle, especially when combined with traceability tools and data-sharing portals. Once a building is completed, AI-driven software can predict when maintenance or repairs will be required based on data gathered during the construction process. This information can be supported on site with scanning technology and augmented reality to make repair or improvement faster and less disruptive. This approach enhances the longevity of the building, reduces maintenance costs and supports a more sustainable use of resources over time.
Automation and robotics
Automation is another growing trend in MMC, particularly within the factory environment. Robots are being used for precision tasks like assembling wall panels, installing insulation or handling repetitive tasks that require high levels of accuracy. Automation also speeds up production, reduces human error and allows for greater customisation of components, making the construction process more efficient.
Conclusion
Embracing MMC should no longer be overlooked as an option but considered a necessity to ensure that the homes we build keep pace with regulatory changes and the rising demand for sustainable housing. As technology continues to evolve, the combination of MMC, AI and sustainable construction practices offers a powerful solution for the future of social housing in the UK and beyond.
But to maximise the impact of offsite requires both a cultural shift in thinking and a greater commitment to embracing new technologies if the industry is to truly deliver on its promises to create quality, affordable homes.
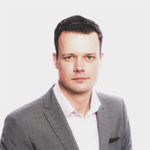
Will Jones is Marketing and Digital Director at Saint-Gobain Off-Site Solutions